Packaging testing refers to the systematic evaluation and analysis of packaging materials, components, and the overall packaging systems, including primary, secondary, and tertiary packaging, to ensure their effectiveness, safety, and compliance with regulatory standards.
It involves a series of tests that assess various aspects such as durability, strength, integrity, protection, and environmental impact.
Materials testing
Answer
What is 'materials testing' and how do you test?
In a packaging context, materials testing refers to the evaluation and analysis of the physical, mechanical, and chemical properties of various materials used in the manufacturing of packaging components, including primary, secondary, and tertiary packaging. The goal of materials testing is to ensure that the chosen materials are suitable for their intended purpose, offer the required level of protection, comply with relevant industry standards, and maintain product integrity throughout the supply chain.
The following are some common types of materials testing conducted in the packaging industry:
-
Tensile strength test
This test measures the maximum load a material can withstand before breaking or deforming under tension. It is crucial for assessing the material's ability to withstand forces during handling and transportation.
-
Burst strength test
The burst strength test evaluates a material's resistance to puncture or rupture when subjected to pressure, simulating conditions experienced during shipping or storage.
-
Compression test
This test examines a material's resistance to compressive forces, essential for determining its stacking capability and ability to protect products from crushing.
-
Flexibility test
The flexibility test assesses how well a material can bend or flex without cracking or breaking. It is essential for packaging materials that need to conform to product shapes.
-
Impact resistance test
This test evaluates how well a material withstands impact or shock, simulating conditions during transportation and handling.
-
Abrasion resistance test
Abrasion testing measures a material's ability to withstand rubbing or scraping, ensuring durability during transportation and stacking.
-
Permeability test
This test assesses the material's resistance to the passage of gases, vapors, or liquids, crucial for packaging materials that need to maintain product freshness or prevent contamination.
-
Chemical compatibility test
This evaluation checks how a material reacts when in contact with specific substances, ensuring it does not interact adversely with the product it contains.
-
Heat and cold resistance test
Materials are subjected to extreme temperature conditions to assess their performance and stability under different environmental circumstances.
-
Environmental sustainability test
This assessment considers the material's impact on the environment, including recyclability, biodegradability, and eco-friendliness.
-
Color and UV stability test
For materials with color or UV-sensitive products, this test determines the material's ability to retain its appearance and protect the contents from UV damage.
By conducting comprehensive materials testing, packaging manufacturers can make informed decisions about the materials they use, optimize packaging design, ensure regulatory compliance, and enhance the overall performance and reliability of their packaging solutions.
What is 'materials testing' and how do you test?
In a packaging context, materials testing refers to the evaluation and analysis of the physical, mechanical, and chemical properties of various materials used in the manufacturing of packaging components, including primary, secondary, and tertiary packaging. The goal of materials testing is to ensure that the chosen materials are suitable for their intended purpose, offer the required level of protection, comply with relevant industry standards, and maintain product integrity throughout the supply chain.
The following are some common types of materials testing conducted in the packaging industry:
-
Tensile strength test
This test measures the maximum load a material can withstand before breaking or deforming under tension. It is crucial for assessing the material's ability to withstand forces during handling and transportation. -
Burst strength test
The burst strength test evaluates a material's resistance to puncture or rupture when subjected to pressure, simulating conditions experienced during shipping or storage. -
Compression test
This test examines a material's resistance to compressive forces, essential for determining its stacking capability and ability to protect products from crushing. -
Flexibility test
The flexibility test assesses how well a material can bend or flex without cracking or breaking. It is essential for packaging materials that need to conform to product shapes. -
Impact resistance test
This test evaluates how well a material withstands impact or shock, simulating conditions during transportation and handling. -
Abrasion resistance test
Abrasion testing measures a material's ability to withstand rubbing or scraping, ensuring durability during transportation and stacking. -
Permeability test
This test assesses the material's resistance to the passage of gases, vapors, or liquids, crucial for packaging materials that need to maintain product freshness or prevent contamination. -
Chemical compatibility test
This evaluation checks how a material reacts when in contact with specific substances, ensuring it does not interact adversely with the product it contains. -
Heat and cold resistance test
Materials are subjected to extreme temperature conditions to assess their performance and stability under different environmental circumstances. -
Environmental sustainability test
This assessment considers the material's impact on the environment, including recyclability, biodegradability, and eco-friendliness. -
Color and UV stability test
For materials with color or UV-sensitive products, this test determines the material's ability to retain its appearance and protect the contents from UV damage.
By conducting comprehensive materials testing, packaging manufacturers can make informed decisions about the materials they use, optimize packaging design, ensure regulatory compliance, and enhance the overall performance and reliability of their packaging solutions.


Component testing
Answer
What is 'component testing' and how do you test?
Component testing, in a packaging context, refers to the evaluation and assessment of individual packaging components that are used in the assembly of the final packaging system.
These components can include various elements such as product packaging (e.g., bottles, tubes, pouches), closures (e.g., caps, lids), tamper-evident closures, seals, labels, and other elements that contribute to the overall functionality, safety, and integrity of the packaging.
The following are some common types of component testing conducted in the packaging industry:
-
Closure Integrity Test
This test evaluates the effectiveness of closures (e.g., caps, lids) in sealing the product packaging and preventing leakage or contamination. It ensures that the closures can maintain their integrity under different conditions.
-
Torque Test
For closures with screw-on caps, the torque test assesses the applied torque required to open or close the closure, ensuring it meets design specifications and consumer usability requirements.
-
Tamper-Evidence Test
Tamper-evident closures are tested to ensure they provide visible signs of tampering or opening attempts, providing an indication of product safety and authenticity.
-
Fitment Test
Fitment testing ensures that various packaging components fit together seamlessly and securely, preventing accidental opening or leakage.
-
Label Adhesion Test
This test assesses the strength and durability of labels on the packaging, ensuring they remain securely attached throughout the product's lifecycle.
-
Compatibility Test
Component materials are tested to ensure they are compatible with the product they will contain, ensuring that no adverse reactions occur that could compromise the product's quality or safety.
-
Extractables and Leachables Test
This analysis identifies and quantifies any substances that could be released from the packaging materials into the product. It helps determine if the packaging is suitable for the specific product and its intended use.
-
Residual Seal Force Test
For seals used in packaging, this test measures the force required to break the seal, ensuring it provides the desired level of tamper resistance.
-
Drop Test (for individual components)
Components, such as closures and caps, may undergo drop testing to assess their resilience and impact resistance.
-
Environmental Stress Crack Resistance (ESCR) Test
This test evaluates the resistance of plastic components to environmental stress cracking, which can be caused by certain substances or environmental conditions.
-
Print Quality and Labeling Test (for individual components): This test verifies the quality of printing on individual components, such as closures and labels, ensuring legibility and compliance with regulatory requirements.
By conducting comprehensive component testing, packaging manufacturers can identify any weaknesses or potential issues in the individual elements that make up the packaging system.
This enables them to make necessary improvements, ensure product safety and functionality, and provide high-quality and reliable packaging solutions to their customers and end-users.
What is 'component testing' and how do you test?
Component testing, in a packaging context, refers to the evaluation and assessment of individual packaging components that are used in the assembly of the final packaging system.
These components can include various elements such as product packaging (e.g., bottles, tubes, pouches), closures (e.g., caps, lids), tamper-evident closures, seals, labels, and other elements that contribute to the overall functionality, safety, and integrity of the packaging.
The following are some common types of component testing conducted in the packaging industry:
-
Closure Integrity Test
This test evaluates the effectiveness of closures (e.g., caps, lids) in sealing the product packaging and preventing leakage or contamination. It ensures that the closures can maintain their integrity under different conditions. -
Torque Test
For closures with screw-on caps, the torque test assesses the applied torque required to open or close the closure, ensuring it meets design specifications and consumer usability requirements. -
Tamper-Evidence Test
Tamper-evident closures are tested to ensure they provide visible signs of tampering or opening attempts, providing an indication of product safety and authenticity. -
Fitment Test
Fitment testing ensures that various packaging components fit together seamlessly and securely, preventing accidental opening or leakage. -
Label Adhesion Test
This test assesses the strength and durability of labels on the packaging, ensuring they remain securely attached throughout the product's lifecycle. -
Compatibility Test
Component materials are tested to ensure they are compatible with the product they will contain, ensuring that no adverse reactions occur that could compromise the product's quality or safety. -
Extractables and Leachables Test
This analysis identifies and quantifies any substances that could be released from the packaging materials into the product. It helps determine if the packaging is suitable for the specific product and its intended use. -
Residual Seal Force Test
For seals used in packaging, this test measures the force required to break the seal, ensuring it provides the desired level of tamper resistance. -
Drop Test (for individual components)
Components, such as closures and caps, may undergo drop testing to assess their resilience and impact resistance. -
Environmental Stress Crack Resistance (ESCR) Test
This test evaluates the resistance of plastic components to environmental stress cracking, which can be caused by certain substances or environmental conditions. -
Print Quality and Labeling Test (for individual components): This test verifies the quality of printing on individual components, such as closures and labels, ensuring legibility and compliance with regulatory requirements.
By conducting comprehensive component testing, packaging manufacturers can identify any weaknesses or potential issues in the individual elements that make up the packaging system.
This enables them to make necessary improvements, ensure product safety and functionality, and provide high-quality and reliable packaging solutions to their customers and end-users.
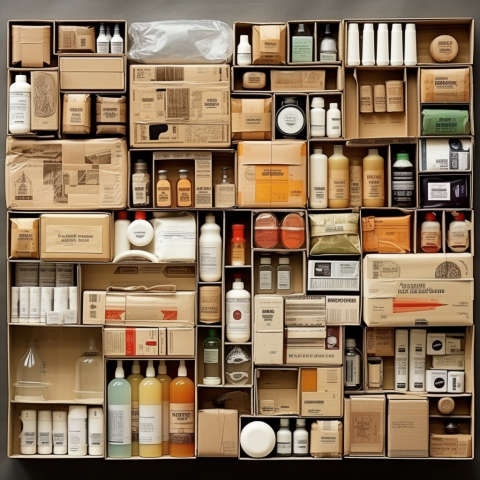

Primary packaging
Answer
What is 'primary packaging' and how do you test?
Primary packaging refers to the immediate layer of packaging that comes into direct contact with the product. It is the first level of containment, meant to protect and preserve the product from manufacturing through distribution to the end-user. Primary packaging can vary depending on the product type and industry and may include materials like bottles, cans, jars, blister packs, pouches, and tubes.
To ensure the quality and functionality of primary packaging, various tests can be conducted:
-
Leakage test
This test checks the primary packaging's ability to prevent leaks or spills. It involves subjecting the packaging to pressure or vacuum, with the presence of a tracer gas or liquid, to detect any leaks.
-
Physical durability test
Primary packaging should withstand typical handling and transportation stresses. This test assesses its resistance to compression, impact, and vibration.
-
Compatibility test
Certain products can react with packaging materials, affecting the product's quality. Compatibility tests examine how the product interacts with the packaging over time.
-
Seal integrity test
For packaging with seals or closures, this test evaluates the effectiveness of the seals in preventing contamination and preserving the product.
-
Child-resistant test
If the product is potentially harmful to children, the primary packaging may be required to pass child-resistant tests to ensure it is difficult for young children to open.
-
Stability and shelf-life testing
Packaging is tested under different storage conditions to evaluate its impact on the product's stability and shelf life.
By performing these tests, manufacturers can identify any issues with the primary packaging and make necessary improvements to ensure it adequately protects the product, meets safety standards, and provides an optimal user experience.
What is 'primary packaging' and how do you test?
Primary packaging refers to the immediate layer of packaging that comes into direct contact with the product. It is the first level of containment, meant to protect and preserve the product from manufacturing through distribution to the end-user. Primary packaging can vary depending on the product type and industry and may include materials like bottles, cans, jars, blister packs, pouches, and tubes.
To ensure the quality and functionality of primary packaging, various tests can be conducted:
-
Leakage test
This test checks the primary packaging's ability to prevent leaks or spills. It involves subjecting the packaging to pressure or vacuum, with the presence of a tracer gas or liquid, to detect any leaks. -
Physical durability test
Primary packaging should withstand typical handling and transportation stresses. This test assesses its resistance to compression, impact, and vibration. -
Compatibility test
Certain products can react with packaging materials, affecting the product's quality. Compatibility tests examine how the product interacts with the packaging over time. -
Seal integrity test
For packaging with seals or closures, this test evaluates the effectiveness of the seals in preventing contamination and preserving the product. -
Child-resistant test
If the product is potentially harmful to children, the primary packaging may be required to pass child-resistant tests to ensure it is difficult for young children to open. -
Stability and shelf-life testing
Packaging is tested under different storage conditions to evaluate its impact on the product's stability and shelf life.
By performing these tests, manufacturers can identify any issues with the primary packaging and make necessary improvements to ensure it adequately protects the product, meets safety standards, and provides an optimal user experience.
Secondary packaging
Answer
What is 'secondary packaging' and how do you test?
Secondary packaging refers to the packaging that contains and protects individual units of a product, bringing together multiple primary packages for storage, transportation, and display purposes. It is the packaging layer that comes after primary packaging and is often used to group products for efficient handling during distribution and retail.
To test secondary packaging, various evaluations and assessments are conducted to ensure its functionality and suitability for the intended purpose:
-
Drop test
This test simulates the package's response to impact during handling and transportation. It involves dropping the package from a specified height to check its ability to protect the primary packages and products inside.
-
Compression test
The secondary packaging is subjected to vertical pressure to determine its ability to withstand stacking and handling in warehouses and during transportation.
-
Vibration test
This test assesses how the secondary packaging responds to vibrations experienced during transportation, ensuring it maintains its integrity and protects the primary packages and products from damage.
-
Stacking test
This evaluation examines how well the secondary packaging supports the weight of multiple packages when stacked together, without collapsing or causing damage to the primary packages and products.
-
Tear resistance test
This test assesses the secondary packaging's resistance to tearing or damage during handling and transit.
-
Edge Crush Test (ECT)
ECT measures the strength of the package's vertical edges to evaluate its ability to withstand crushing forces.
-
Box Compression Test (BCT)
BCT assesses the resistance of the entire box structure to compression forces, simulating the pressures experienced during stacking and transportation.
-
Environmental testing
Secondary packaging may be subjected to temperature and humidity variations to ensure it remains effective under different environmental conditions.
-
Print quality and labeling test
This evaluation verifies the quality of printing on the secondary packaging, including barcode readability and label adherence.
-
Packaging efficiency and design review
Assessing the overall design and efficiency of the secondary packaging, such as the optimal use of materials, ease of assembly, and cost-effectiveness.
-
Sustainability assessment
An evaluation of the secondary packaging's environmental impact, considering factors like recyclability and use of eco-friendly materials.
By conducting these tests, manufacturers can identify weaknesses in the secondary packaging design and make necessary adjustments to ensure it provides adequate protection to the primary packages and products during transportation and storage, as well as meets industry standards and regulations.
What is 'secondary packaging' and how do you test?
Secondary packaging refers to the packaging that contains and protects individual units of a product, bringing together multiple primary packages for storage, transportation, and display purposes. It is the packaging layer that comes after primary packaging and is often used to group products for efficient handling during distribution and retail.
To test secondary packaging, various evaluations and assessments are conducted to ensure its functionality and suitability for the intended purpose:
-
Drop test
This test simulates the package's response to impact during handling and transportation. It involves dropping the package from a specified height to check its ability to protect the primary packages and products inside. -
Compression test
The secondary packaging is subjected to vertical pressure to determine its ability to withstand stacking and handling in warehouses and during transportation. -
Vibration test
This test assesses how the secondary packaging responds to vibrations experienced during transportation, ensuring it maintains its integrity and protects the primary packages and products from damage. -
Stacking test
This evaluation examines how well the secondary packaging supports the weight of multiple packages when stacked together, without collapsing or causing damage to the primary packages and products. -
Tear resistance test
This test assesses the secondary packaging's resistance to tearing or damage during handling and transit. -
Edge Crush Test (ECT)
ECT measures the strength of the package's vertical edges to evaluate its ability to withstand crushing forces. -
Box Compression Test (BCT)
BCT assesses the resistance of the entire box structure to compression forces, simulating the pressures experienced during stacking and transportation. -
Environmental testing
Secondary packaging may be subjected to temperature and humidity variations to ensure it remains effective under different environmental conditions. -
Print quality and labeling test
This evaluation verifies the quality of printing on the secondary packaging, including barcode readability and label adherence. -
Packaging efficiency and design review
Assessing the overall design and efficiency of the secondary packaging, such as the optimal use of materials, ease of assembly, and cost-effectiveness. -
Sustainability assessment
An evaluation of the secondary packaging's environmental impact, considering factors like recyclability and use of eco-friendly materials.
By conducting these tests, manufacturers can identify weaknesses in the secondary packaging design and make necessary adjustments to ensure it provides adequate protection to the primary packages and products during transportation and storage, as well as meets industry standards and regulations.
Tertiary packaging
Answer
What is 'tertiary packaging' and how would you test it?
Tertiary packaging refers to the outermost layer of packaging used to protect and transport large quantities of products or goods. It is designed to contain multiple units of secondary packaging, which, in turn, hold individual products or smaller groups of items. Tertiary packaging is commonly used in shipping and warehousing to facilitate the handling and distribution of goods in bulk.
Examples of tertiary packaging include pallets, stretch wrap, corrugated boxes, large containers, and other materials used to secure and group secondary packages. The main purpose of tertiary packaging is to ensure the safe transportation and storage of products, while also simplifying the logistics and handling process.
Testing tertiary packaging is crucial to guarantee the safety and integrity of the products during transportation and storage. Several key tests can be performed to evaluate the effectiveness of tertiary packaging:
-
Compression test
This test assesses the package's ability to withstand vertical pressure, simulating stacking during shipping or storage. It helps ensure that the products inside are protected from crushing or damage.
-
Vibration test
The packaging is subjected to simulated vibrations to imitate the conditions during transportation. This test helps identify potential weaknesses and ensures the packaging remains intact.
-
Drop test
A drop test involves intentionally dropping the packaged product from a specified height to assess the packaging's ability to protect the goods from impact during handling or transit.
-
Stacking test
This test examines how the packages behave when stacked on top of each other. It helps identify if the tertiary packaging can support the weight of multiple layers without collapsing or causing damage to the products inside.
-
Environmental test
Tertiary packaging may be exposed to different environmental conditions during transportation, such as temperature and humidity changes. Testing under various environmental conditions helps ensure the package's integrity.
-
Transportation simulation
This comprehensive test involves replicating the actual transportation conditions, including vibration, temperature variations, and rough handling. It assesses the overall performance of the tertiary packaging system.
-
Distribution cycle test
This test evaluates the packaging's ability to endure the complete distribution cycle, from manufacturer to retailer or end-user, including loading, unloading, and intermediate handling.
By conducting these tests and making necessary improvements, manufacturers can ensure that their tertiary packaging provides adequate protection to the products throughout the supply chain, reducing the risk of damage and maintaining product quality.
What is 'tertiary packaging' and how would you test it?
Tertiary packaging refers to the outermost layer of packaging used to protect and transport large quantities of products or goods. It is designed to contain multiple units of secondary packaging, which, in turn, hold individual products or smaller groups of items. Tertiary packaging is commonly used in shipping and warehousing to facilitate the handling and distribution of goods in bulk.
Examples of tertiary packaging include pallets, stretch wrap, corrugated boxes, large containers, and other materials used to secure and group secondary packages. The main purpose of tertiary packaging is to ensure the safe transportation and storage of products, while also simplifying the logistics and handling process.
Testing tertiary packaging is crucial to guarantee the safety and integrity of the products during transportation and storage. Several key tests can be performed to evaluate the effectiveness of tertiary packaging:
-
Compression test
This test assesses the package's ability to withstand vertical pressure, simulating stacking during shipping or storage. It helps ensure that the products inside are protected from crushing or damage. -
Vibration test
The packaging is subjected to simulated vibrations to imitate the conditions during transportation. This test helps identify potential weaknesses and ensures the packaging remains intact. -
Drop test
A drop test involves intentionally dropping the packaged product from a specified height to assess the packaging's ability to protect the goods from impact during handling or transit. -
Stacking test
This test examines how the packages behave when stacked on top of each other. It helps identify if the tertiary packaging can support the weight of multiple layers without collapsing or causing damage to the products inside. -
Environmental test
Tertiary packaging may be exposed to different environmental conditions during transportation, such as temperature and humidity changes. Testing under various environmental conditions helps ensure the package's integrity. -
Transportation simulation
This comprehensive test involves replicating the actual transportation conditions, including vibration, temperature variations, and rough handling. It assesses the overall performance of the tertiary packaging system. -
Distribution cycle test
This test evaluates the packaging's ability to endure the complete distribution cycle, from manufacturer to retailer or end-user, including loading, unloading, and intermediate handling.
By conducting these tests and making necessary improvements, manufacturers can ensure that their tertiary packaging provides adequate protection to the products throughout the supply chain, reducing the risk of damage and maintaining product quality.
Transport/logistics testing
Answer
What is 'transport/logistics testing' and how do you test?
[NEEDS COPY WRITTEN] Tertiary packaging refers to the outermost layer of packaging used to protect and transport large quantities of products or goods. It is designed to contain multiple units of secondary packaging, which, in turn, hold individual products or smaller groups of items. Tertiary packaging is commonly used in shipping and warehousing to facilitate the handling and distribution of goods in bulk.
Examples of tertiary packaging include pallets, stretch wrap, corrugated boxes, large containers, and other materials used to secure and group secondary packages. The main purpose of tertiary packaging is to ensure the safe transportation and storage of products, while also simplifying the logistics and handling process.
What is 'transport/logistics testing' and how do you test?
[NEEDS COPY WRITTEN] Tertiary packaging refers to the outermost layer of packaging used to protect and transport large quantities of products or goods. It is designed to contain multiple units of secondary packaging, which, in turn, hold individual products or smaller groups of items. Tertiary packaging is commonly used in shipping and warehousing to facilitate the handling and distribution of goods in bulk.
Examples of tertiary packaging include pallets, stretch wrap, corrugated boxes, large containers, and other materials used to secure and group secondary packages. The main purpose of tertiary packaging is to ensure the safe transportation and storage of products, while also simplifying the logistics and handling process.